Lean manufacturing is the manufacturing model proposed by the Massachusetts Institute of Technology in 1990, and this production model has been applied to the manufacturing workshop of Toyota Motor Corporation in Japan as early as the 20s century and has been successfully used today.
Its core content is to reduce the waste of resources within the enterprise and obtain the maximum output with the minimum input. The ultimate goal is to respond most quickly to market needs with products of the best quality and lowest cost.
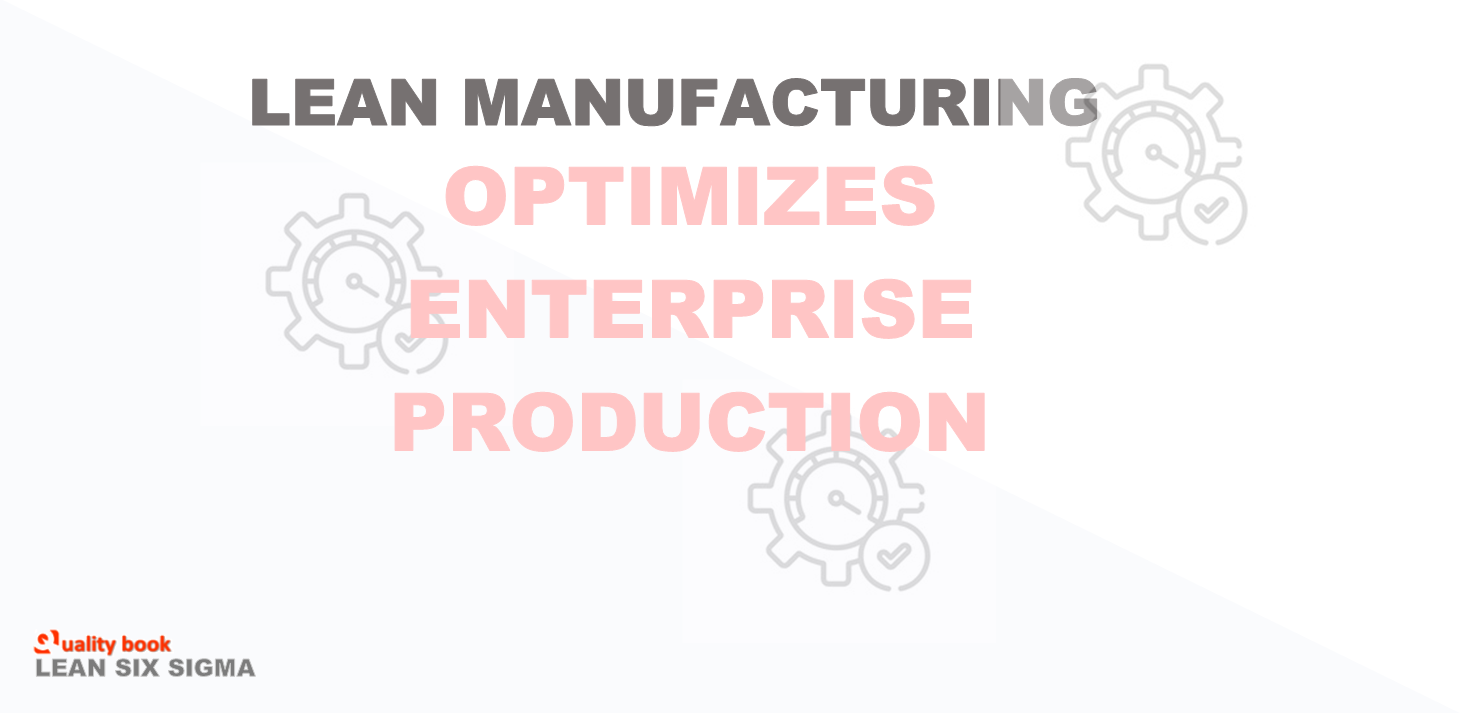
The origins of lean manufacturing
In the process of exploring new production models, Toyota found that small batch production costs less than mass production, and there are two reasons for this phenomenon:
First, small batch production does not require the large amount of inventory, equipment, and personnel of mass production;
Second, only a small number of parts are produced before assembly, and errors can be corrected immediately. Based on the latter reason, Toyota concluded that the inventory time of products should be controlled to less than two hours, which is the prototype of just-in-time production (JIT) and zero inventory.
In fact, JIT production was later extends to cooperation with partners. Defining the close dependence between manufacturing companies and partners in this model.
In order to detect and correct errors at any time. It is necessary to have working groups composing of highly skills, and highly responsible workers. In the assembly line production mode. The workers on the assembly line only repeat some simple actions. But are not responsible for the quality of the product. And the production quality is inspected by the special inspection department after the overall assembly of the product. But in fact, the workers on the assembly line know the situation on the first line best. If the errors in production are corrects on the assembly line. There will be no large-scale disassembly and repair due to the accumulation of errors.
Group Management
Therefore, Toyota divides workers into groups according to production. Each group corrects the errors in the production process of this group at any time. The regularly collectively discusses and puts forward suggestions for improving the process flow. Which is the early form of group technology and quality control.
Of course, the assembly line always stopped when the practice of correcting errors at any time was implemented. But when all the working groups grasped the frequent errors, and had some experience in discovering the causes of them. The number of errors was greatly reduced.
Because the workers in each work group are responsible for their production. They have the right to decide how to increase productivity levels, and implement improvement measures themselves. Which means that workers have the power to make decisions. In terms of empowering production teams. In addition to giving them the right to improve production. The team leader is also given strong administrative power, and the team leader can promote outstanding members based on the performance of the team members.
This management style has changed the production culture of the enterprise and laid the foundation for the development of lean manufacturing models in the future.
Reducing waste of resources is central.
Lean thinking and waste are direct opposites. Waste includes many types, such as:
Idle inventory, unnecessary processes, unnecessary transportation of goods, production that exceeds demand, unnecessary transfer of personnel, various waits, etc.,
All these activities that may be rarely noticed in daily production, are opposed by lean thinking, and strive to eliminate. From the acquisition of orders by the company to the production process to the final sale, the idea of eliminating waste runs throughout.
In order to eliminate waste, the “pull” production method has emerged, which is the opposite of the traditional “push” principle.
From meeting the needs of customers to the internal production process, it is adopted in this way: The production needs of the factory are determined by the customer, and when the production is carried out, how each production process is produced is determined by the needs of the next production process, and if there is no demand, additional products must not be produced, thus eliminating additional inventory.
This kind of “pull” production in enterprise production is usually achieved through the “Kanban” mechanism.
Kanban Mechanism
Each production process confirms whether the next “customer” has a request through the “Kanban”, and only when there is a request is the production carried out. JIT is based on this “pull” supply mechanism, that is, with the right parts, good quality, the right quantity, at the right time, to provide production, only when the production is needed, the right materials are called.
The JIT mechanism was later used to work with suppliers, so that most of the producer’s supplies could be stored with the supplier, thereby reducing the manufacturer’s own inventory.
Within the enterprise, unnecessary transportation between workshops is also a waste, and effectively setting the sequence of production workshops can eliminate this waste. Similarly, the location determination within the shop floor should be arranged around the process design of the production team.
Eliminating waste is at the heart of lean thinking, and just-in-time production and zero inventory are the main ways to reduce production costs and shorten production cycles.
In addition, total quality management is the main measure to ensure product quality and achieve the goal of zero defects, and group technology is the technical basis for achieving multi-variety, organizing production according to customer orders, expanding batch and reducing costs. It can be said that just-in-time production, total quality control, and group technology are the main pillars of lean manufacturing.
BPCS lean manufacturing process
In June this year, SSA GT launched “Lean Manufacturing Process (LMP)” as part of BPCS (Business Planning and Controlling System). Becoming the first ERP manufacturer to offer an integrated solution for ” lean manufacturing “. Which is good news for companies looking to move to lean.
Due to the limitations of the lean manufacturing model itself. It is more suitable for manufacturing enterprises with relatively stable product production and operating environment. That is to say, it is suitable for production processes with relatively fixed process routes and fixed products. Such as automobiles, home appliances and other industries. Because of this, LMP can adapt to both make-to-order and make-to-order businesses.
Cell Manufacturing
In make-to-order enterprises, it is based on cell manufacturing and pull systems. Once the customer order is accepted, it is included in the workload of the production cell. The new “cell workbench” program allows the production planner. To adjust the planning and production of the customer order within the manufacturing cell and place the order for production.
The whole process does not need to go through the main production planning, planned order creation, planned order release, etc. All production is planned and controlled by customer orders. The cell workbench can display orders pending release by date with a comparison chart of unit load and capacity status by day. The rescheduling of orders dynamically adjusts the load chart.
When actually producing, the actual control in each production cell is obtained through “kanban” instead of a shop order with a production list. Production reports can be carried out at the finished product level against customer orders and have component (material) and standard manual multi-level backflushing functions. According to the production report, the item is automatically assigned to the customer order, which can be shipped.
For order-to-order items, a purchase order is automatically placed after the customer order is accepted. When a purchase order is received, the item is automatically assigned to the customer order to which it belongs, and the order is put into a pickup state.